Bioaugmentation
- Rick Fuller
- Jan 2, 2019
- 10 min read
Updated: Mar 18, 2021
Detailed Review of Bioaugmentation
Bioaugmentation is the addition of a specially prepared bacterial culture to a bioreactor (aeration tank, oxidation ditch, etc.). The goal of bioaugmentation includes objectives such as: 1) increasing the density of more desirable bacteria, 2) achieving a specific operational goal such as degrading complex organic compounds, 3) increasing the overall organic removal rate, and 4) recovering from an upset in the biological treatment system.
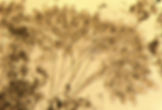
Many wastewater operators in particular are faced with difficult operating conditions and stringent discharge permits that challenge the capability of their wastewater treatment plant. Under these conditions bioaugmentation can be a cost-effective, short-term, or medium-term solution to maintain effluent compliance until system changes and/or plant upgrades can be implemented. In other cases, bioaugmentation can be a long-term, cost-effective solution because of the lack of capital funds and the expense of system upgrades which often requires an expansion of the biological treatment system including the costly installation of additional aeration (oxygen generation) capacity.
Biological Wastewater Treatment
In aerobic biological treatment systems, aerobic (and facultative) bacteria utilize oxygen in the degradation (oxidation) of organic compounds. The dissolved oxygen (DO) concentration, pH, mixed liquor suspended solids (MLSS) concentration, sludge age (MCRT), food-to-microorganism (F:M) ratio, and nutrient level (nitrogen and phosphorus) are some of the critical parameters that determine the successful operation of a biological system. Historically, process control has focused on monitoring and controlling these parameters with little attention given to the nature and composition of the microorganisms beyond an occasional quick view of the MLSS under a microscope.
The microorganisms (or biomass) in the bioreactor are the workers in a wastewater treatment system. The biomass is always in a state of flux, with different microbes dying while others are growing and becoming more dominant. Under adverse or stressed conditions such as toxicity, variable pH, low DO, excessive COD loading, and high (or low) wastewater temperature, certain bacterial populations may be reduced or eliminated, causing poor effluent quality. Under these stressful conditions biological systems can be very slow to recover. Bioaugmentation is designed to address the problem of slow biomass recovery and to supplement reduced or lost bacterial populations.
A prevailing belief has been that, over time, hardy, efficient, fully-acclimated, ideal microorganisms will populate the activated sludge system. This approach assumes that the indigenous or existing bacterial population introduced via routes such as windblown solids, rainwater, and the plant influent stream will always contain the best-suited, most optimized microorganisms. In reality, even though the natural microorganism population may develop into an acceptably-performing biomass, there may be performance limitations that can only be overcome through the introduction of superior strains of specially-cultured microorganisms.
In the bioreactor of an industrial wastewater treatment plant you can expect to find numerous strains of bacteria. This bacterial diversity is necessary because some types of bacteria degrade different compounds more effectively and efficiently than others. These bacteria generally are well suited to handle the contaminants in the wastewater and will become acclimated, over time, to provide a sufficient degree of treatment, assuming a steady-state operation is achieved. But few, if any, industrial wastewater systems ever achieve steady-state operating conditions.
The nature and composition of industrial waste streams change frequently. Variation in the wastewater composition may be due to changing production schedules, cleaning of process equipment, chemical spills in the production plant, or mechanical problems with equipment. Because of this variability, many industrial wastewater treatment systems have biological populations that neither grow to optimum levels nor achieve the required bacterial diversity. In these situations bioaugmentation becomes a valuable tool that can be utilized by the wastewater operator to improve the performance of the biological treatment system.
Cultured Bacteria
Bioaugmentation is the use of select microbial strains (cultured bacteria) that have been isolated from the environment to improve or enhance the operation of a biological wastewater treatment system.
With bioaugmentation, cultured bacteria are used to enhance the performance of the existing microorganism population with bacteria that have greater, and more robust, capabilities. Cultured bacteria are isolated from environmental samples (wastewater, biosolids, compost, and/or soil) and selected by conventional enrichment techniques. The cultured bacteria are grown in a nutrient-rich media that contains a specific organic chemical as the sole source of carbon and energy or as the sole source of nitrogen (for bacteria cultured to initiate or enhance nitrification). Bacteria that can handle relatively high concentrations of the target chemical are selected. The selected bacterial strains are grown in large fermenters followed by concentration in a centrifuge. The bacteria are then preserved by drying. The cultured bacteria are able to withstand extreme environmental conditions including organic overload, complex, refractory or hard-to-degrade organics, swings in wastewater temperature, pH extremes, reduced dissolved oxygen levels, limited nutrients, and outright toxicity.
Typical bioaugmentation products consist of blends of several strains of microorganisms, usually bacteria or fungi. The microorganisms are isolated from nature and are not genetically altered in any way. They are selected on the basis of accelerated reproduction rates and their ability to perform specific functions, such as good floc-forming capabilities to enhance settling in a clarifier or the ability to degrade specific compounds. The products are sold in a variety of forms, with dried microorganisms on a bran carrier and liquid products being the two most common.
Cultured bacteria are grown to degrade difficult, complex, biodegradable compounds. Cultured bacteria and their enzyme systems are more efficient in degrading a larger variety of substrates (measured as chemical oxygen demand or COD, 5-day biochemical oxygen demand or BOD5, and/or total organic carbon or TOC) than bacteria common to activated sludge systems. The cultured bacteria have unique abilities that enable them to survive and remain active under harsh environmental or operational conditions that are not tolerated as well by other bacteria.
Cultured bacteria can efficiently degrade readily degradable COD (chemical oxygen demand) as well as difficult-to-degrade COD. The cultured bacteria can compete more effectively for available nutrients and dissolved oxygen in the wastewater than the existing or indigenous bacterial population and filamentous microorganisms. Perhaps more importantly, bioaugmentation products can be used to treat a variety of toxic wastes. Examples of industrial wastes that contain inhibitory or toxic compounds that can be treated with bioaugmentation products include a variety of synthetic and natural organic chemicals and compounds such as acetone, acrylic acid, ammonia, nitrite, furfural, phenolic compounds, and methyl ethylamine, to name just a few.
Several areas where bioaugmentation has proven to be beneficial are…
Enhanced COD Removal: Many wastewater treatment plants must deal with increased flows and loadings and more complex waste streams, stressing and exceeding the capacity of the biological system. It can cost millions in capital to upgrade and expand these systems. By increasing the microbiology numbers and diversity of the microbial population through bioaugmentation, significant improvements in COD reduction can be achieved.
Improved Solids Settling: An important step in biological wastewater treatment is solids removal, usually through settling of the MLSS in a secondary clarifier. Bacteria form, and secrete, natural biopolymers (sticky polysaccharides) that aid in settling through the formation of larger, denser, floc particles. Too many inhibitory compounds, too much food (COD), or outright toxic shocks to the biological system will result in a bacterial population with little biopolymer secretion, dispersed floc formation, and poor settling characteristics. The effectiveness of adding organic polymers or inorganic coagulants as settling aids is often reduced when the bacterial population is stressed due to overfeeding (excessive COD) and/or the presence of inhibitory compounds. By inoculating the system with microorganisms known to be both resistant to the toxicity and excellent floc formers, polymer demand can be reduced while its effectiveness in aiding sludge settling remains high.
Preferential Degradation of Specific Compounds: By adding selected bacteria, low levels of particular compounds can be achieved in the effluent from the biological treatment system that are not possible with the indigenous or existing microbial population. Compounds such as phenols, chlorinated aromatics, and aromatic hydrocarbons are just a few of the many compounds that can be reduced with bioaugmentation.
Improved Nitrification: Many industrial wastewater plants have difficulty in achieving nitrification because of design limitations, stressful conditions such as variable pH, inhibitory compounds, or toxic shocks. By regularly adding nitrifying bacteria, the proper bacterial population required for ammonia removal can be maintained.
Other Areas: Other areas where bioaugmentation be beneficial include odor reduction, oil and grease removal, rapid system start-up, and improved tolerance to toxic shock.
Bioaugmentation Dosage Rates
There are several different approaches that can be taken when implementing a program of bioaugmentation. Some wastewater plants simply add one pound of bugs per day to their biological reactor and will, based on operator experience, increase the quantity (to 5, 10, or more pounds per day) if there is a significant increase in effluent COD when there has not been a corresponding decrease in the mixed liquor suspended solids (MLSS) concentration or a reduction in biological reactor detention time. The daily addition of a bioaugmentation product is basically a “maintenance” dose used to keep the biological system healthy regardless of the variation in the wastewater being treated.
When there has been no prior bioaugmentation, a more formal or mathematical approach can be taken in response to correcting a poorly operating biological (activated sludge) system. In this case, bacterial cultures are added to a treatment unit (the aeration tank, bioreactor, biotreater, etc.) at a higher introductory dose followed by a lower dose which is maintained until effluent quality has improved. If an introductory dose is used, the dose is usually ≥2 ppm up to 4 ppm or more and may be applied for 2-4 days before reducing the dosage rate. In most cases the maintenance dose is approximately ≤2 ppm and may be applied daily, weekly, or as needed.
Bioaugmentation Dosage Rate Calculations
Two approaches are shown for calculating the bioaugmentation dosage rate. The first method is the conventional, simple approach, which is based on using the influent flow rate to the biological system. The second approach is based on supplementing the quantity of biomass already in the bioreactor using the volume of the bioreactor (aeration tank) as the basis for determining the quantity of bugs to add. These calculations are applicable to all aerobic biological treatment systems. Some extra time will be spent here detailing dosage rate calculations because very little information can be found on how to do this. Surprisingly, even the makers of cultured bacteria provide little insight regarding the use of their bioaugmentation products.
The bioaugmentation dosage rate is typically in the range of 1 to 10 mg/L. The initial or starting dosage rate, which is determined as a function of treatment conditions, is selected to jump start the bioaugmentation process. The worse current conditions are, the higher the starting dosage rate.
Assumptions
Flow rate: 3,000 gallons per minute (4.32 million gallons per day)
Bioreactor volume: 2,500,000 gallons
MLSS concentration: 3,200 mg/L
Initial bioaugmentation dosage rate: 4 mg/L (or 4 ppm)
Method 1: Influent Flow Rate Approach
This approach is straightforward, relying on one of the most fundamental wastewater calculations used by operators, as shown in the equation below.
Pounds of bugs to add per day

So, for example, a 12-day bioaugmentation program might consist of two days at 4 ppm (144 lb/day) followed by three days at 2 ppm (72 lb/day) with the final seven days at a dosage rate of 1 ppm (36 lb/day) requiring a total of 756 pounds of bugs (cultured microorganisms). This is shown graphically below.
Bioaugmentation Feed Rate
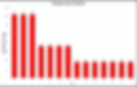
Method 2: Bioreactor Volume Approach
The volume of the bioreactor in this example is 2,500,000 gallons. Using this volume as the basis for establishing the initial dosage rate, beginning at 4 ppm of bacterial addition to start the bioaugmentation process, we derive the following dosage rate in units of pounds per day, as shown in the equation below. Note that the calculation of 4 ppm represents 4 parts of cultured bacteria per million parts of wastewater in the bioreactor. Stated another way, we are adding 4 pounds of bugs for every million pounds of wastewater in the bioreactor.
Initial Dosage Rate

Given the set of assumptions stated above, using Method 1, the starting bioaugmentation dosage rate was calculated to be 144 pounds on the first day. Using Method 2, the starting dosage rate was significantly less at just 83 pounds on the first day, representing a 42.4% reduction in the bioaugmentation feed rate. So how do we account for such a large difference between the two methods? Which method is the correct one?
For the choice of method there is no right answer when it comes to bioaugmentation. A simple rule-of-thumb might be: The more pounds of bugs added, the faster will be the improvement in effluent quality. How quickly a high level of effluent quality is achieved might be driven by a need to meet discharge permit requirements. In this case, Method 1 would be the preferred or recommended approach. When economics are a major factor in the bioaugmentation process and the discharge permit is not at risk of being violated, Method 2, a more conservative, more economical approach, would be recommended. If the treatment goal is less ambitious, in that we are only looking to improve the general health and viability of the microbial population in the bioreactor, we would implement bioaugmentation using a maintenance program with a 1 or 2 ppm dosage rate.
Overdosing/Under-dosing
When implementing a program of bioaugmentation you cannot overdose, no matter how many bugs you add. Rather, the more bugs you add, the sooner you will see positive, favorable results in effluent quality. The primary issue with overdosing is cost. Bioaugmentation is not an inexpensive endeavor so cost control is always a concern. A secondary issue with overdosing is that bioaugmentation typically results in the need to increase sludge wasting once conditions in the bioreactor improve and the COD removal rate increases. An increase in sludge wasting and the associated increase in sludge disposal represents another cost increase for the treatment plant.
Bioaugmentation Spreadsheet
You can download a simple Excel spreadsheet to assist in calculating bioaugmentation dosage requirements here. The inputs required to determine the dosage rates are shown in the screenshot below.
Monitoring the Bioaugmentation Program
Depending on the laboratory equipment available to you, the effectiveness of the bioaugmentation program can be determined by the following monitoring and control procedures:
Track the mixed liquor suspended solids (MLSS) concentration daily and, preferably, the mixed liquor volatile suspended solids (MLVSS) concentration to better indicate changes in the quantity of microorganisms in the bioreactor.
Perform a “general” microscopic analysis every few days to observe changes in the microorganisms in the MLSS.
Measure the influent and effluent COD from the bioreactor and calculate the percent removal looking for a steady increase in the COD removal rate.
Measure the total suspended solids (TSS) and/or turbidity of the supernatant in a settled MLSS sample, after 30 minutes of settling time, and track the improvement in this value.
Based on the settled sludge volume in an MLSS sample that has settled for 30 minutes, using a 1 liter settleometer, compute the sludge volume index (SVI). For the best settling with the highest quality turbidity in the clarifier overflow we are looking for an SVI ≤150 mL/g.
Measure the oxygen uptake rate in the overflow leaving the bioreactor daily.