API Separator
- Rick Fuller
- Oct 21, 2016
- 9 min read
Updated: Feb 7, 2024
Oil-Water Separation
Though municipal wastewater treatment plants have to deal with their share of oil and grease (O&G), this post on oil-water separation applies more to industrial wastewater systems, particularly those associated with petrochemical plants.
There are several variables that can significantly influence the performance of gravity oil-water separators which include: 1) flow rate [velocity through the separator], 2) oil gravity [density], 3) pH, and 4) temperature of the wastewater. Being close to, or below, the design flow rate (velocity through the unit ≤3 feet per minute [fpm]) is critical for optimal performance. Lower pH (<7) enhances oil removal compared to higher pH (≥7). And as the wastewater temperature increases, oil removal through the unit will be improved.

Some Characteristics of Oil
Crude oil quality is measured in terms of density (light to heavy) and sulfur content (sweet to sour). Density is classified by the American Petroleum Institute (‘API’). API gravity is defined based on density at a temperature of 15.6 ºC. The higher the API gravity, the lighter the crude. Light crude generally has an API gravity of 38 degrees or more, and heavy crude an API gravity of 22 degrees or less. Crude with an API gravity between 22 and 38 degrees is generally referred as medium crude.
Oil in wastewater is frequently colloidal. Colloidal species encountered in raw water and wastewater include clay, silica, iron and other heavy metals, color, and organic solids. The removal of colloidal materials in the wastewater moving through an oil-water separator can be enhanced with of polymer added to the separator influent. Different vendors have different chemical preferences with some recommending the use of a coagulant (iron or aluminum product). My personal recommendation is to use a high-charge, high molecular weight, cationic flocculant.
Gravity oil-water separators are primarily intended to remove free oil as defined below. These units are not designed to remove emulsified oil. Emulsified oils may contain other contaminants such as solids, silt, metal particles, emulsifiers, cleaners, soaps, surfactants, and solvents. Reducing the pH, typically below 6, helps to break emulsions as does increasing the temperature of the wastewater.
Oil removal rates are shown in the two tables below.
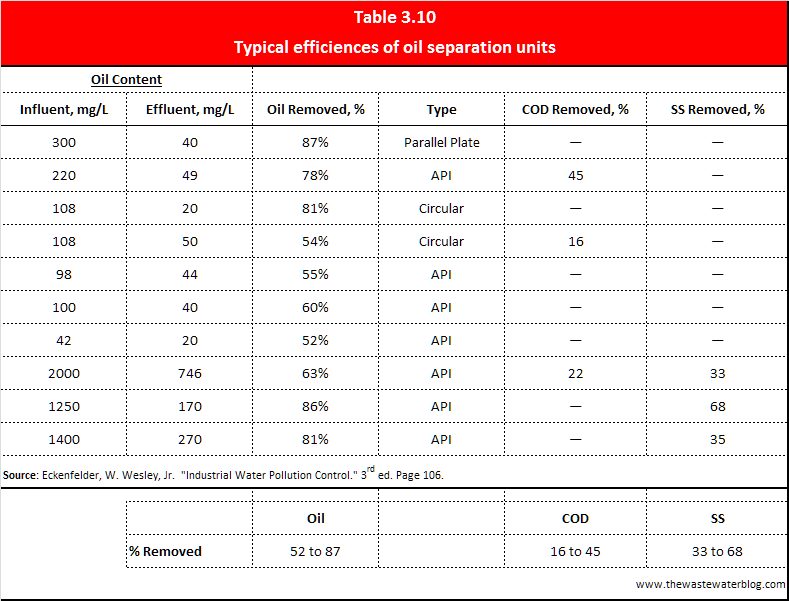

API Separator
The API separator is normally the first, and arguably, most important wastewater treatment step in petroleum refineries. The primary function of a properly designed API separator is to remove the majority of oil and suspended solids from refinery wastewater before it enters downstream wastewater treatment processes. For years, refineries have attempted to use other technologies or treatment scenarios as an alternative to the API separator. But most refineries ultimately select, or return to, the API separator as the technology of choice for their wastewater treatment primary oil/solids separation step. (Note: API stands for American Petroleum Institute.)
A refinery wastewater may contain oil in three forms and all three forms may be present in a given waste stream. The three forms of oil encountered in wastewater are:
Free oil
Emulsified oil
Dissolved oil
Discrete oil globules will rise due to buoyant forces to form an oil layer on top of the water. This makes them relatively easy to remove in an API separator or they can be skimmed from the surface in an Equalization tank. Free oil can be removed by gravity separation which is what the API separator is designed for. Removal is a function of flow conditions, differences in specific gravity, temperature, and the stability of the oil. Coarse oily solids with a specific gravity >1.0 will settle to the bottom of the separator which is why bottom scrapers or flights are included in along with a conical hopper to collect the settled solids.
Emulsified oil is comprised of oil droplets with a diameter of less than 20 microns, mostly in the 1–10 micron range. Emulsified oil is a stable suspension in the water due to inter-particle forces dominating buoyant forces. Emulsified oil will not separate from the water under quiescent conditions aided by gravity, the very conditions created in an API separator. The removal of emulsified oil requires chemical addition such a pH adjustment to drop the pH or emulsion breakers. Once treated in this way the wastewater often enters a dissolved air (or nitrogen) flotation unit to remove the emulsified oil as it begins to break from the wastewater.
Dissolved oil forms a true molecular solution with water and cannot be removed by gravity separation. Dissolved oil removal requires biological treatment.
The API separator, shown in the graphic below, has become the generic name for “conventional oil-water separators.” Conventional oil-water separators can only remove free oil. Stable emulsions and dissolved oil require additional treatment.

API separators are designed to achieve an oil concentration leaving the separator of not more than 200 ppm, though oil concentration values closer to 50 ppm can often be obtained. Additional API separator performance parameters are:
Oil Reduction: 52 – 99%
COD Reduction: 5 – 45%
TSS Reduction: 10 – 68%
Measuring the oil & grease (O&G) concentration into, and/or out of, an API separator is not always feasible so I have often used chemical oxygen demand (COD) as a surrogate parameter to estimate the oil reduction through an API.
When the oil removal through the API is not sufficient, a secondary unit process, such as induced gas flotation (IGF), corrugated plate interceptor (CPI), or dissolved air or nitrogen flotation (DAF or DNF) will follow the API separator to provide a “polishing” step to significantly reduce the oil loading to the downstream biological treatment system. Free oil is a "desirable" food source for microorganisms in biological treatment units and as such, if the oil concentration is too high, the oxygen supply to the bioreactor can prove to be insufficient creating a low dissolved oxygen condition which ultimately will reduce treatment plant performance.
Note: In many refineries you will only find an IGF, CPI, or DNF instead of an API separator. The refinery wastewater system shown in the graphic below does not have an API separator, using a CPI unit, after the equaliztion tank, instead.
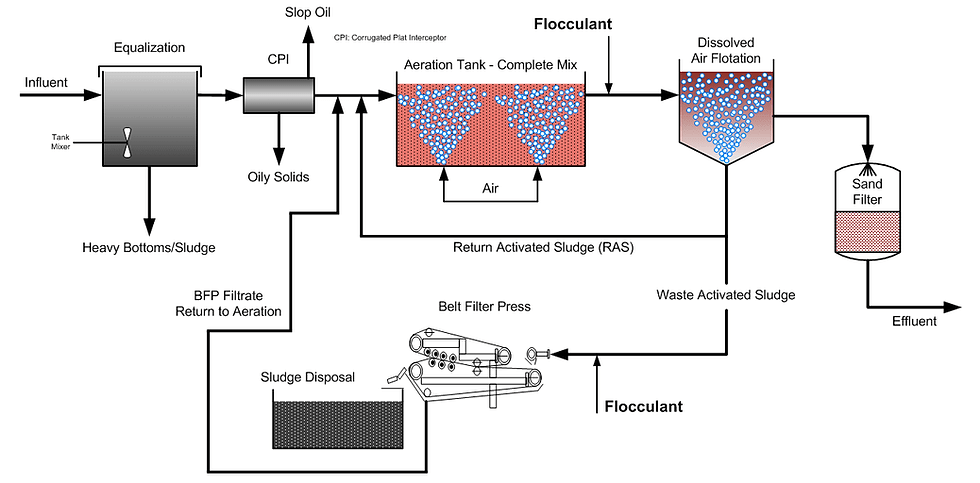
Stokes Law
The API separator is a gravity separation device that works on the principle of Stokes Law, which defines the rise velocity of an oil particle based on its density and size. Typically, the difference between the specific gravity of oil to be separated and water is much closer than the specific gravity of the suspended solids and water. Therefore, the design of the API separator is based on the difference in the specific gravity of the oil to be separated and the wastewater. If this design criterion is followed, the majority of suspended solids will settle in the unit. Once the oil and suspended solids are removed from the wastewater in the API separator, the middle phase, water, is then sent on for further treatment in most refinery wastewater treatment plants.
API Performance Factors
Key factors influencing API separator performance include water temperature, horizontal velocity, the density and size of the oil droplets, and the quantity and characteristics of the suspended solids. API separators are designed to remove oil droplets with diameters as small as 0.015 cm (150 microns). In addition, API separators are designed to maintain laminar flow. Under most operating conditions, the API separator will remove both free oil and suspended solids down to a concentration of between 50 and 200 mg/L. The removal of other contaminants, including chemical oxygen demand (COD) and total suspended solids (TSS), is variable. COD removals in the range of 16 to 45% and TSS removals in the range of 33 to 68% have been documented. Removing the bulk of free oils, greases, and suspended solids from the wastewater reduces overloading and other problems in downstream treatment processes.
API Separator Design Criteria
The design standards for the API separator have been well documented and can be found in the current edition of API Specification 421. Some of the most important design criteria developed for API separators include:
Length to width ratio: A minimum length to width ratio of 5:1 is recommended for all API separator designs to keep operating conditions as close to plug flow as possible, minimizing the potential for short circuiting.
Depth to width ratio: A minimum depth to width ratio of 0.3 to 0.5 is recommended so that separation units are not excessively deep; minimizing the amount of time it takes for oil particles to rise to the surface.
Maximum channel width and depth: The maximum API separator channel width is 20 ft; maximum depth is 8 ft.
Horizontal velocity: Maintaining a horizontal velocity of no more than 3.0 ft/min has been shown to minimize turbulence and its effect on interfering with the separation of oil from wastewater.
Inlet distribution: To minimize the effect of high wastewater inlet velocities into the API separator, and possible short-circuiting associated with these high velocities, reaction jet baffles are recommended to diffuse influent flows across the width and depth of the API separator.
Oil particle size: Majority of oil particles in most refinery wastewaters are 150 micron in size or larger. Therefore, the design standards for API separators were developed for the removal of oil particles of this size. Particles smaller than 150 micron will normally exit an API separator and will need to be removed by downstream treatment processes, unless allowances are made in the sizing of the API separator to remove these smaller particles.
A process flow diagram for a “complete API separator system" is shown below. In my experience, one of the biggest problems I see with ALL separators, whether API, CPI, DAF, DNF, or IGF, is the failure to remove settled solids regularly, frequently, from the bottom of these critical unit processes. Too often, because solids removal is not frequent enough, for a long enough period of time, solids/sludge removal becomes inoperable and the plant just gives up. As a result, the flight skimming system breaks (chains, flights, etc.) and solids continue to accumulate on the bottom of these tanks. Gradually, the volume of the tank is decreased which then increases the velocity through the tank which further reduces the performance of these units. When I have to troubleshoot API separators the first question I ask is: How often do you remove bottom solids?
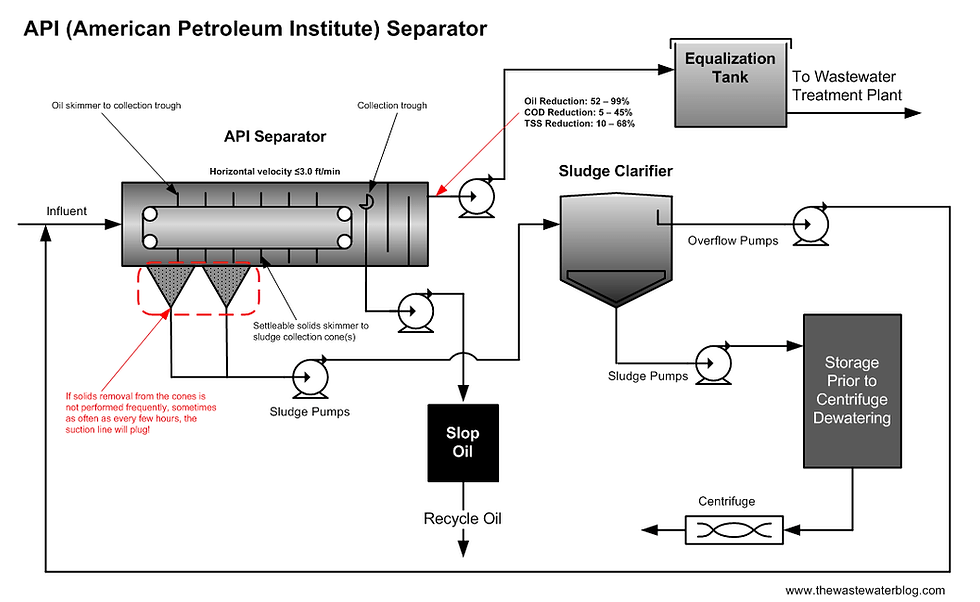
It may be a little hard to see some of the details in the schematics above. You can download a PowerPoint and/or a PDF of these graphics below. The PowerPoint appears to have better graphics because the conversion of the PowerPoint to a PDF file seemed to reduce the images somewhat.
Important Note: One of the key parameters for the operation of an API separator is the horizontal velocity (VH). The horizontal velocity should not exceed 3 feet per minute (fpm) or 0.91 meters per minute. Please pay attention to this number and the units: feet per MINUTE. I have found many websites where the horizontal velocity value is listed as 3 feet per second. This is incorrect!! I think some people are thinking of the recommended velocity of wastewater in a pipeline, such as a gravity sewer, which recommends a higher velocity, which I describe below in the section titled: "Velocity of Wastewater in a Sewer Line."
The following is a quote from the “Design and Operation of Oil-Water Separators” API Publication 421, First Edition, February 1990:
“Although some separators may be able to operate at higher velocities, 3 feet per minute has been selected as a recommended upper limit for conventional refinery oil-water separators. Most refinery process-water separators operate at horizontal velocities much less than 3 feet per minute at average flow. All separators surveyed had average horizontal velocities of less than 2 feet per minute, and more than half had average velocities less than 1 foot per minute, based on typical or average flow rates.” (pg. 4)
Velocity of Wastewater in a Sewer Line
The wastewater in a sewer line should move at a speed which will prevent the deposition and buildup of solids in the sewer; this is called a “scouring velocity.” Experience has shown that wastewater velocities of two feet per second or greater will keep solids usually contained in wastewater moving in a sewer line. A scouring or self-cleaning velocity may not be attainable during periods of minimum daily flows. However, a sewer should be designed to produce a scouring velocity during the average daily flow or, at the very least, during the maximum daily flow. (Source: California State University, Sacramento. Operation and Maintenance of Wastewater Collection Systems. 3rd ed. Volume 1. 1987.)
Grit Channels
The simplest means of removing grit from the wastewater flow is to pass it through channels or tanks which allow the velocity of flow to be reduced to a range of 0.7 to 1.4 ft/sec (0.2 to 0.4 m/sec). The objective is to allow the grit to settle to the bottom while keeping the lighter organic solids moving along to the next treatment unit. Experience has shown that a flow-through velocity of one foot per second (ft/sec) is best.
All particles settle at different rates based on their size and weight. Most grit chambers are designed to remove 0.2 mm size sand and all other heavier materials. Experiments have shown this size particle will settle downward at about 0.075 ft/sec. This means that if wastewater if flowing in a channel at a depth of one foot and a particle of 0.2 mm is introduced at the surface, it will take:

If this waste were flowing at one foot per second, it would travel for 13.3 seconds, or a distance of 13.3 feet, before the particle reached the channel bottom. It the waste were flowing at a depth of three feet in the channel, it would take 13.3 seconds/ft × 3 ft = 39.9 seconds or 39.9 feet before the particle reached the bottom. (Source: California State University, Sacramento. Operation of Wastewater Treatment Plants. 4th ed. Volume 1. 1998.)
Comments